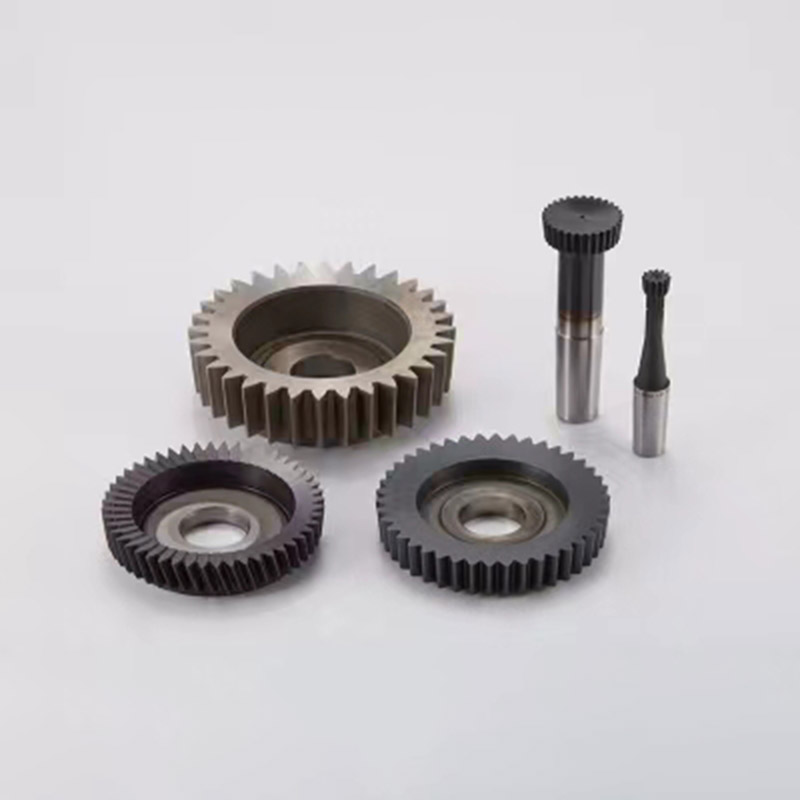
防止拉刀的断裂即刀齿损坏:拉削时由于刀齿上受力过大,拉刀强度不够,是损坏拉刀的主要原因。造成刀齿受力过大的因素:拉刀齿升量过大、拉刀弯曲、切削刃各点拉削余量不均匀、刀齿径向圆跳动大、预制孔太粗糙、材料内部有硬质点、工件强度过高、严重粘屑和容屑槽挤塞以及工件夹持偏斜等。1)要求预制孔精度IT10~IT8、表面粗糙度Ra≤5µm,预制孔与定位端面垂直度偏差不超过0.05mm。2)严格检查拉刀的制造精度。3)拉削高性能和难加工材料,可选取适当热处理改善材料 的加工性,也常使用高性能材料的拉刀或涂层拉刀。4)保管、运输拉刀时,防止拉刀弯曲变形和破坏刀齿。
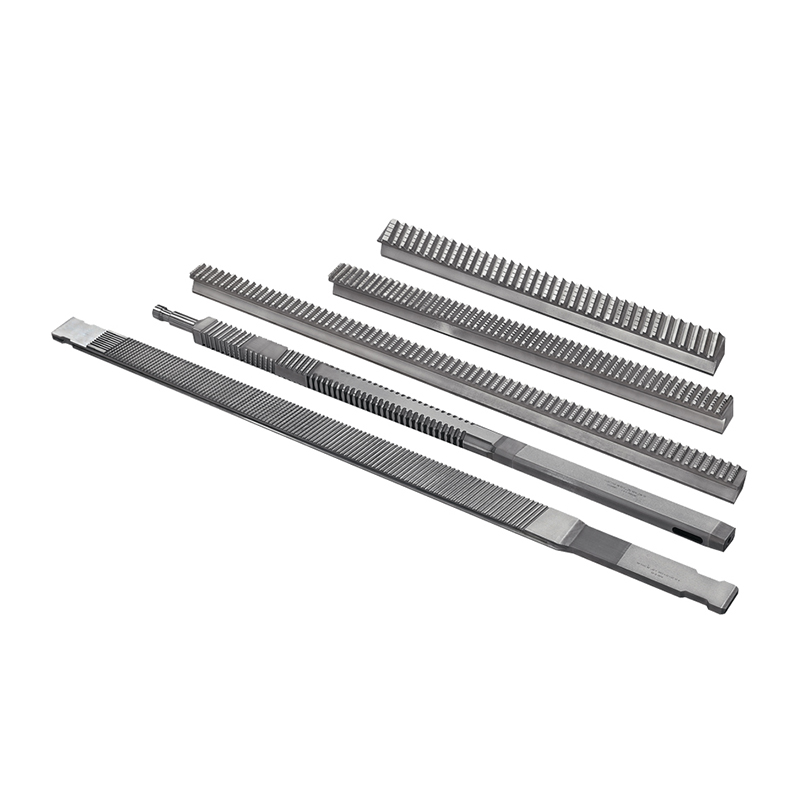
拉刀的设计特点:加工具有复杂廓形的外表面时,通常将拉刀设计为组合式,行将若干把拉刀安装在1个刀体上,使其分别加工同1零件的各部份表面。组合拉刀中的各把拉刀既可同时工作也可顺次工作。设计组合拉刀时,首先需将待加工表面廓形划分成若干简单的单元。为使加工每单元的拉刀设计最简化,同时又能提高拉削效力和缩短拉刀长度,在廓形分段及拉刀配置时应斟酌尽量让几把拉刀同时参与工作,但这样常常会造成拉刀结构过于复杂、拉刀及其紧固件布置困难、拉床过载、零件加工时变形过大、排屑困难等问题,因此在多数情况下采取同时加工与顺次加工相结合的方式来安排拉刀位置,公道拉削复杂表面。
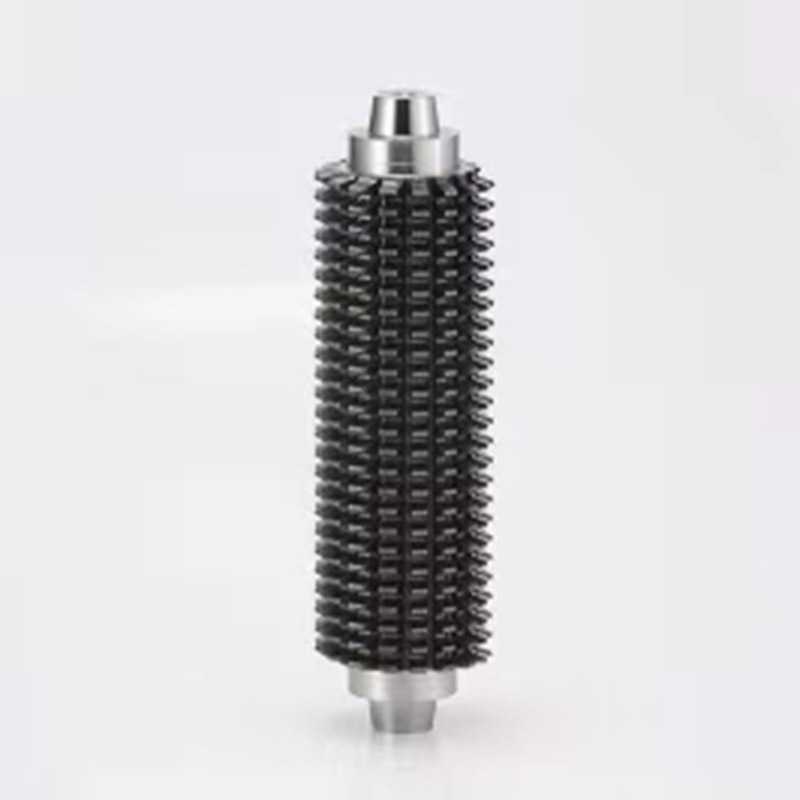
拉刀是用于拉削的成形刀具。刀具表面上有多排刀齿,各排刀齿的尺寸和形状从切入端至切出端依次增加和变化。当拉刀作拉削运动时,每个刀齿就从工件上切下一定厚度的金属,最终得到所要求的尺寸和形状。拉刀常用于成批和大量生产中加工圆孔、花键孔、键槽、平面和成形表面等,生产率很高。拉刀按加工表面部位的不同,分为内拉刀和外拉刀;按工作时受力方式的不同,分为拉刀和推刀。推刀常用于校准热处理后的型孔。